Scheduling production at times when material supply is a constraint

by Juha Lunkka • 5 min read
During the last couple of years, it has been easy to notice that the availability of even commodity products has been much more limited than usual. Try to order a new car with decent delivery time for instance.
Obviously there are many underlying reasons behind the phenomena – global shortage of semiconductor components, lack of shipping containers in the supply chain network, Covid related bottlenecks in logistics operations especially in China to name a few.
More complexity, more constraints to take care of
Manufacturers in the Nordics are operating today mostly in make-to-order, configure-to-order and engineer-to-order modes. Often that means material procurement based on customer orders as well. Volume production without a worry about material availability constraints is a dream from the past for most of the manufacturing companies. Balancing the demand and supply is currently very challenging and that brings also implications to operative production scheduling. One study from machinery industry shows e.g. numbers like orders +44%, lead times >100%, production +6% (Q1/22 compared to Q1/21). That means a challenging equation.
Manufacturing is basically straightforward. Take some material in, refine it, take care of quality assurance, pack it and ship it on time. And don´t forget to send the invoice. In real life, it´s everything but easy, given the competitive environment of today. Orchestrating elements like cost, quality, productivity, amount of product variants, new product introductions, changes in product definitions/bill of materials, delivery time, materials and resources availability – and in the end customer satisfaction being the most important one.
In this article we are mostly looking the topic from the materials and resources availability and scheduling perspective. “How much and when some specific material will be available at the factory´s goods receiving” – that´s one relevant question when creating a valid production schedule in a manufacturing company. Even after this, typically the amount of available materials to factory floor will change after the receiving inspection. The inspection yield rarely being 100%. That has an effect on your production schedule.
Build the situational visibility and perform schedule changes on time
We know we have lots of uncertainties in material availability. If you don´t have all the needed materials available for specific work order, it doesn´t make much sense to place it in work queue. Unfortunately, quite often we identify material shortages in very late moment – sometimes after the work order is already in progress. Improving starts from providing the visibility to real life situation.
Time is the enemy. Also in production planning and scheduling everything starts from the process. Doing the right things, right way, in optimal sequence. Modern planning and scheduling software may be the missing link. The most commonly used scheduling tool on top of ERP – collection of spreadsheets, maybe supercharged with some macros – is highly flexible. But nothing comes without a price tag.
Having many dependencies and industry scale amount of orders it becomes impossible to keep the schedule up-to-date within reasonable response time. Without capability to reschedule quickly based on material constraints often means executing a production schedule which is lacking some materials. And that means in the end waste in the process and more work-in-progress at the shop floor.
When making a production schedule based on real life constraints – not only running a Material Requirements Planning in ERP – it´s possible to identify material and capacity problems before they realize. When running different scenarios, it´s also often feasible to consider the urgency and priority of customer orders and related work orders. Some orders tend to be such that there´s no way they can be late and some others might not be that critical. Meaning even with slight delay there wouldn´t be direct customer harm present – that might be the case with e.g. delayed stock replenishment order.
When unlucky incidents are inevitable, customer wants to know them rather soon than late. Might be for instance that your customer needs the product at construction site and therefore there needs to be up-to-date information when product can be installed and when installation related resources, tools, lifting equipment etc. are needed. Due to material shortages, we usually cannot fully avoid delayed customer deliveries. Utilizing today´s capabilities we can at least minimize the negative impacts.
Constraint based production scheduling wasn´t invented yesterday. Technology has been in place for a good while, but now we can see rapid movement in the utilization of it. As we speak, solutions are evolving rapidly and e.g. machine learning algorithms are entering the shop floor.
Paving the ways forward to minimize the impact of material shortages
Based on our experience:
1. Performing production scheduling on a system not taking into account real time availability of materials and other relevant constraints leads to a missing link in your operational excellence agenda
2. It is possible to see problems caused by material shortages in customer orders in advance, so there is still an opportunity to try to solve them before they realize
3. Scenario planning for different situations is easy. The scenario that turns out to be the best is immediately available on the factory floor
4. Large implementation projects are not required. The first improvements are typically achieved in a short period of time and return on investment is quick. Concrete results can be achieved in couple of months
5. There is an opportunity to improve on time delivery, efficiency, lead time and customer satisfaction by utilizing the opportunities brought by Advanced Planning and Scheduling (APS) software
When having a dialogue with our customers, we quite often agree that the first concrete step towards Industry 4.0 themed smart manufacturing is to increase the clock speed in production planning and scheduling – based on the visibility to material and resource constraints.
ideal grp can help you to take your production scheduling to next level!
We are ready to discuss with you about your current state, ambitions and plans – together we will find the improvement path. Let´s have a chat!
More posts

Metso aiming to improve supply chain collaboration through system simulation
Webinar (THIS WEBINAR WILL BE HELD IN FINNISH LANGUAGE) (Material will be distributed in English) August 22, 2023 – 09:00 CET Learn how Metso utilizes system simulation in their hydraulic system design. Research engineer Jesse Backman shares his learning path to system simulation, and how Metso could improve the collaboration of the supply chain through […]

Metso pyrkii kehittämään toimittajayhteistyötä systeemisimuloinnin avulla
Webinaari 22.8.2023 – 10:00 EET Tule kuulemaan kuinka Metso hyödyntää systeemisimulointia hydraulijärjestelmien suunnittelussa. Tutkimusinsinööri Jesse Backman kertoo oppipolkunsa systeemisimuloinnin pariin ja kuinka Metso voisi kehittää yhteistyötä toimittajaketjussaan systeemisimuloinin avulla. Tärkeimmät opit esitellään käytännön suunnitteluesimerkin avulla. Kuinka parantaa yhteistyötä toimitusketjussa systeemisimuloinnin avulla? Mitä systeemisimulointi on? Systeemisimulointi yhdistää yksittäisten komponenttien ominaisuudet ja vuorovaikutukset koko järjestelmän dynaamiseksi käyttäytymiseksi. […]
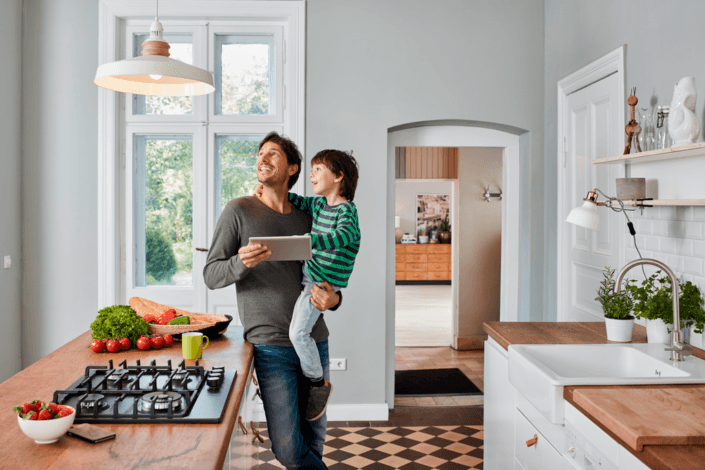
From Chaos to Clarity: Embracing Modularity
by Olli Uuttu • 8 min read Dear reader, have you ever wondered what goes into building a truly modular product? It’s not as easy as it may seem. While there are several proven methods available to plan and implement optimal modular architectures, it still takes effort, dedication, and discipline to succeed. I’m sure you […]